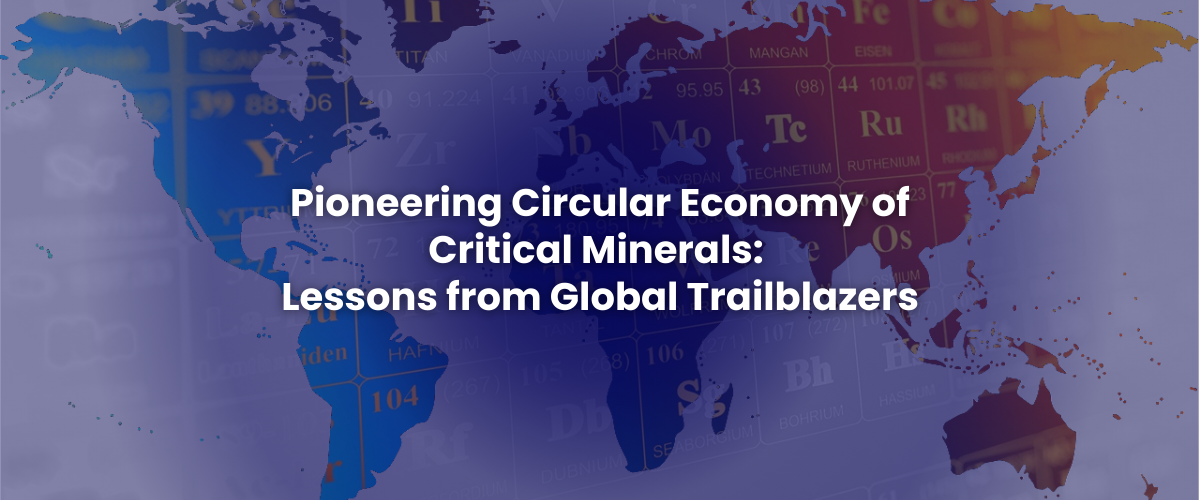
Table of Contents
Lithium ion batteries (LiBs) have become the backbone of modern energy storage, powering everything from smartphones to electric vehicles (EVs) and stationary energy storage systems. However, their lifecycle – from raw critical minerals extraction to disposal – poses significant environmental challenges that innovators worldwide are racing to find solutions for.
This edition of the Lohum Blog explores these challenges, the role of circular critical minerals, and success stories from around the world. Understanding these impacts and exploring innovative solutions & actions through the lens of circular economy principles is crucial for ensuring that every energy transition has a solid, sustainable foundation.
The Environmental Necessity of Closed-loop Critical Minerals for LiBs
The journey of a lithium ion battery begins with the extraction of critical minerals such as lithium, cobalt, nickel, copper, and manganese. This phase is marked by intensive mining practices that have historically led to environmental degradation and humanitarian crises. Open-pit mining disrupts ecosystems and contributes to soil erosion, while brine extraction depletes vital freshwater resources and can introduce toxic chemicals into local environments. Mining and processing these critical minerals is also energy-intensive, often relying on fossil fuels. It is estimated that about 40% of the climate impact from LiB production arises from these activities, with mining operations in regions like China contributing significantly to greenhouse gas emissions due to their reliance on coal.
During the manufacturing process, the production of lithium ion battery packs involves assembling various components into cells, and modules. This stage is characterized by high energy consumption, with the average production of a 28 kWh battery generating approximately 3,061 kg CO₂-equivalent emissions. The manufacturing process also generates hazardous waste, including solvents and heavy metals, which can contaminate water supplies if not managed properly. Even during the usage phase, the environmental benefits of using LiBs are contingent upon the energy sources used to charge them. In regions where electricity is derived from coal, the overall carbon footprint remains significant, diminishing the positive impact of these batteries.
The most pressing environmental challenge lies in the end-of-life disposal of LiBs. An Australian study featured on IER noted that a staggering 98.3% of batteries were disposed of in landfills, leading to the potential leaching of toxic substances like heavy metals into soil and groundwater. This not only poses risks to human health but also increases the likelihood of landfill fires that can burn uncontrollably for extended periods. Additionally, the complexity and variability in battery designs make recycling difficult and costly, often leading manufacturers to prefer newly mined materials over recycled ones.
Why Critical Minerals Cannot Afford a Linear Lifecycle
A linear lifecycle – characterized by a “take-make-dispose” model – is unsustainable for critical minerals due to resource depletion, environmental pollution, and economic inefficiencies. The continuous extraction of finite resources like lithium, cobalt, and nickel leads to increased scarcity and environmental degradation. Each stage of a linear lifecycle also contributes to pollution – whether through mining waste or e-waste from discarded batteries.
As demand for batteries grows with the rise of EVs and renewable energy technologies, failing to implement circular practices will result in higher costs associated with raw material procurement and environmental remediation. This underscores the need for a transformative approach that emphasizes sustainability and resource efficiency.
Embracing Circularity to Mitigate Environmental Impact
The concept of circularity offers a solution to the challenges posed by critical minerals. By embracing circular economy principles, we can mitigate the environmental impacts associated with LiBs while creating a resilient ecosystem.
One key aspect is designing batteries for longevity. Modular design, where batteries can be easily disassembled for repairs or upgrades, can extend their useful life and reduce waste. Additionally, developing batteries with fewer rare materials or those that can be sourced sustainably reduces dependence on harmful mining practices, improving the overall material efficiency.
Enhanced recycling techniques are also crucial. Implementing advanced recycling technologies, such as closed-loop recycling systems and innovative hydrometallurgical processes, can recover valuable materials from spent batteries more efficiently and safely. Governments are beginning to mandate recycling practices through legislation, creating a market incentive for these initiatives.
Repurposing used batteries for second-life applications, such as stationary energy storage, extends their useful life while reducing waste. This not only contributes to a circular economy but also creates new economic opportunities.
Success Stories in Critical Mineral Circularity
Several countries have emerged as leaders in integrating renewables into their energy systems while addressing the challenges posed by critical minerals. These nations have developed innovative policies and practices that promote recycling, circularity, and sustainable management of battery resources.
Norway stands out as a global leader in renewable energy, with approximately 98% of its electricity generated from renewable sources, primarily hydropower. The country has established a comprehensive recycling system for batteries, including LiBs, achieving a high recycling rate. Norway’s commitment to circular economy principles extends beyond recycling; it includes promoting the use of second-life applications for EV batteries in energy storage systems.
Sweden is slated to be fossil fuel-free by 2040. The country has made significant strides in integrating clean energy sources and is only left with 23.8% fossil fuels in its energy mix as of 2025. The country has implemented strict regulations for battery disposal and recycling, with a focus on recovering valuable materials from used batteries. Swedish companies are also at the forefront of developing technologies for efficient battery recycling, such as hydrometallurgical processes that recover lithium and cobalt from spent batteries.
Germany is known for its ambitious renewable energy goals, achieving around 60% of its electricity generation from renewables by 2025. The German government has established regulations mandating the recycling of batteries. The country also invests heavily in R&D for battery technologies and recycling methods, fostering innovation that enhances the sustainability of critical mineral usage.
Costa Rica is a celebrated pioneer in renewable energy, as the nation generates over 98% of its electricity from renewables. Costa Rica’s commitment to environmental sustainability extends to an increasing focus on responsible battery disposal and recycling capabilities. The country also promotes public awareness about the importance of recycling batteries through media aimed at encouraging responsible disposal practices among citizens.
China, the world’s largest producer of renewable energy, is also leading in Lithium ion battery production and critical mineral recycling. The Chinese government has recognized the environmental challenges posed by critical minerals and is investing heavily in recycling infrastructure. China aims to recycle used LiBs through policies that encourage manufacturers to establish take-back programs. The country’s commitment to circular economy principles includes developing second-life applications for EV batteries and enhancing material recovery processes.
Denmark, which generated half its electricity from renewable sources in 2020, has implemented policies that promote the collection and recycling of batteries. The country achieved an electronics recycling rate of 79.9% in 2021 according to reports featured on Statista, supported by initiatives that encourage manufacturers to take responsibility for end-of-life management. Denmark also integrates battery storage solutions into its renewable energy strategy, facilitating better grid stability and energy management.
India is advancing its critical mineral supply chain through the National Critical Mineral Mission (NCMM) and Budget 2025-26 initiatives. With an allocation of Rs 34,000 crore over seven years, the NCMM aims to source 10% of India’s annual critical mineral demand domestically by 2031, with the inclusion of recycling. The budget also proposes eliminating customs duties on scrap containing critical minerals to boost domestic manufacturing and recycling. Additionally, the government is developing a policy to recover critical minerals from tailings and plans a Rs 1,500-crore incentive scheme to attract mineral recycling clusters. These efforts are set to enhance the recycling industry, promote investment in processing facilities, and lessen reliance on primary raw materials, supporting India’s clean energy transition. A circular economy approach could reduce primary critical mineral demand in India by nearly 18% by 2030.
What We Learn
These nations exemplify how integrating renewables with effective critical mineral management can lead to sustainable energy systems. By prioritizing circular economy principles – such as robust, supportive, and profitable recycling programs, second-life applications for batteries, and stringent Extended Producer Responsibility regulations – these countries have set benchmarks that can be built upon.
The transition towards a circular economy for critical minerals is not merely an environmental imperative but also an opportunity for innovation and economic growth. By rethinking how we design, use, and dispose of these essential technologies, we can mitigate their environmental impacts while fostering sustainability.
As we explore and appreciate nuances and success stories in critical mineral circularity, we move closer to realizing a world where our energy ecosystems contribute positively to our planet. The circular economy of critical minerals made possible at Lohum inspires us to dream of sustainability that can indeed perpetuate itself indefinitely in harmony with nature.
Related blogs
This entrepreneur wants India to make its own lithium-ion cells for electric vehicle batteries
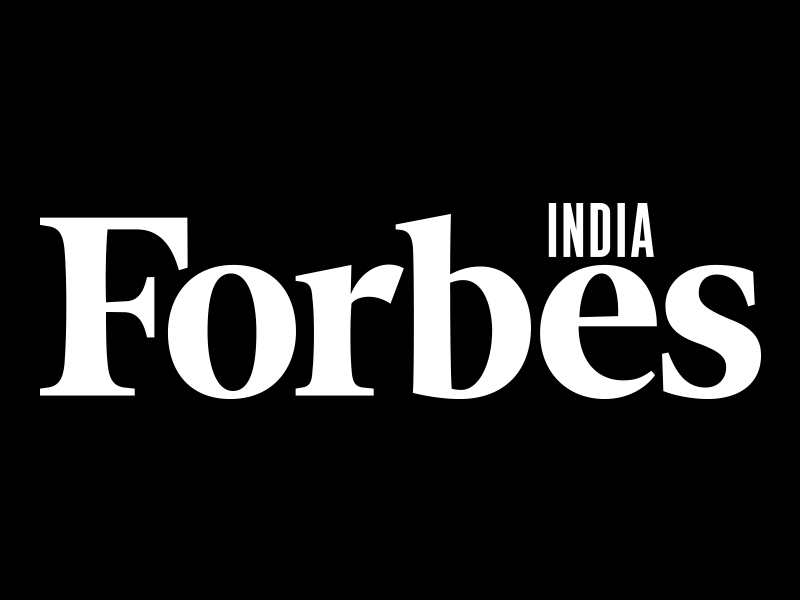
Forbes India
Rajat Verma already recovers raw materials from used cells at his venture, LOHUM Cleantech. He wants to close the loop by making cells in India as well.
India needs integrated recycling and repurposing battery business model: Rajat Verma of LOHUM Cleantech
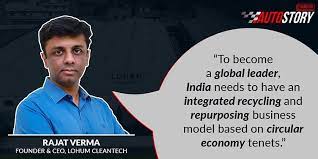
YOURSTORY
In an interaction with AutoStory, Rajat Verma, Founder and CEO of LOHUM Cleantech, speaks about building his company, and about battery manufacturing and repurposing as an industry.
Sourcing Raw Materials Is A Big Challenge In Li-ion Battery Space: Founder Lohum
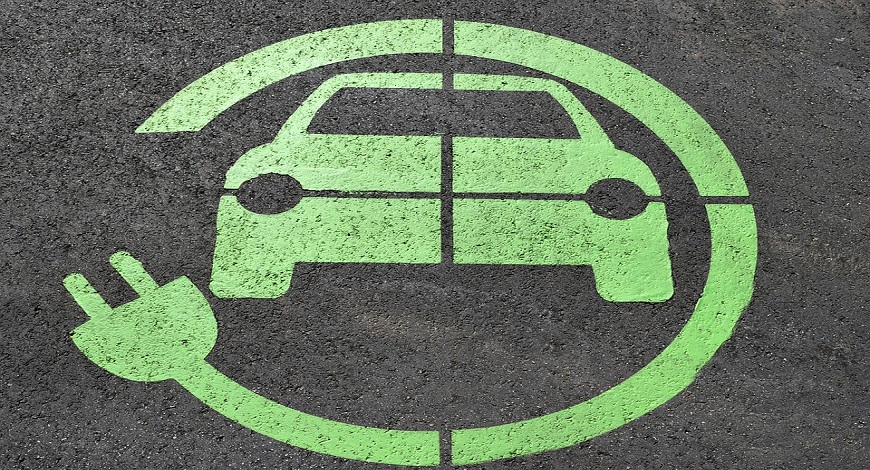
Business World Disrupt
Recognized as ‘The Most Innovative Company of the year 2022’ by The Confederation of Indian Industry (CII), LOHUM is a producer of sustainable Li-ion battery raw materials