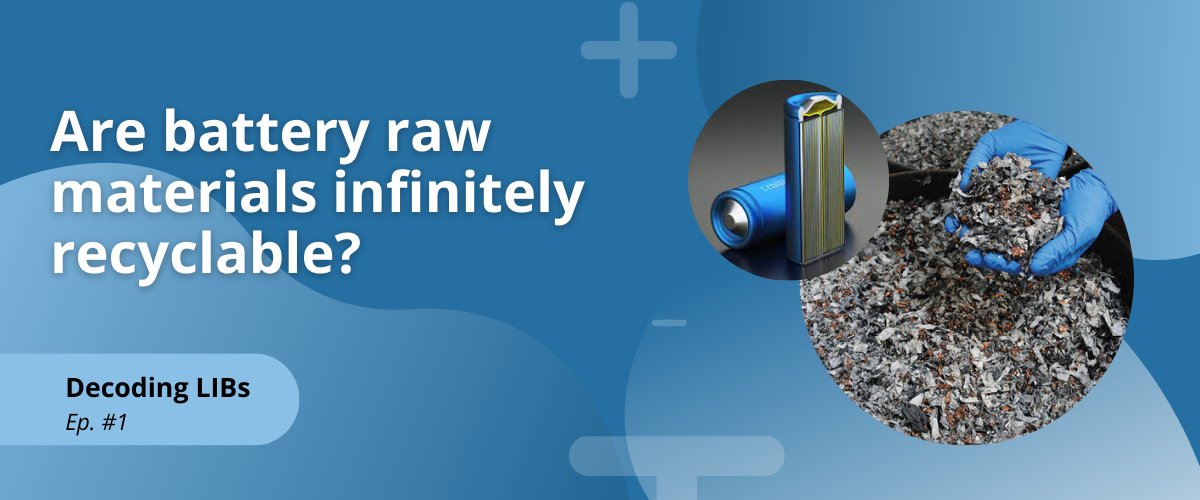
Table of Contents
As the global demand for sustainable energy solutions continues to grow and the world looks increasingly to battery recycling and reuse, the viability of recycled Lithium battery raw materials becomes a critical factor in achieving a low carbon circular economy. In our quest to make battery raw materials last forever, we are often asked the questions: “Are battery raw materials really infinitely recyclable? If so, how is that possible?” and “Does recycling battery produce materials as good as virgin mined materials?”
We sat down with Gazanfar Safvi, Head of Recycling & Chemicals at LOHUM, to answer these questions, delve into the viability of battery material recycling, and explore the potential of recycled materials compared to newly mined ones in this exclusive read.
Battery Raw Material : From Mined to Recycled
Gazanfar explains that battery metals, starting from the mining stage, go through a series of transformations. They are processed from black mass and converted into salts, which are then reacted to create battery molecules. When a battery reaches the end of its life after a second life, the recycling process undertakes the extraction and recovery of these elements. Remarkably, the extracted elements exist as the same salts derived from mining, making them indistinguishable from their virgin counterparts. This means that the recycled salts can be recomposed into new battery molecules for the production of brand new Lithium-ion batteries.
A 2021 report by the International Energy Agency (IEA) on the clean energy transition also emphasized that the recyclability of battery raw materials will play a crucial role in achieving a circular economy and reducing environmental impacts. The report emphasizes the importance of extended producer responsibility in promoting efficient battery recycling practices and ensuring the sustainable management of Lithium-ion batteries throughout their life cycle, and predicts that recycled materials will
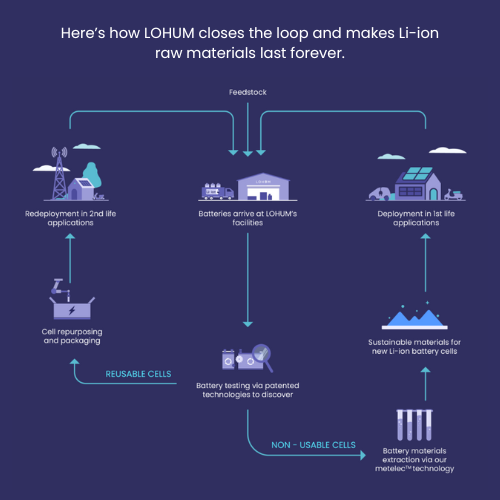
Battery Raw Material Recycling Process: A Breakdown
The processes and technologies used to produce recycled materials broadly vary from Hydro-metallurgical and Pyro-metallurgical to mechanical or direct recycling processes, each of which varies in its CO2e efficiency, economic viability, and yield. LOHUM's NEETM™ for instance is a hydro-metallurgical lithium-ion battery material recycling and extraction technology, which means that this technology uses liquid solutions such as acids to leech out or 'precipitate' the battery metal salts as well as impurities with high recovery rates.
How spent batteries can be recycled:
- Sorting and Disassembly: batteries are sorted based on chemistry, make, etc., and then the battery pack is disassembled into its parts.
- Mechanical shredding: Cells are crushed and shredded to expose the internal components, such as electrolytes.
- Hydro/Pyro-metallurgical processing and Heat Treatment: Certain mechanical and chemical extraction processes are utilized to recover cathode material and salts.
- Purification: The liquid waste generated undergoes treatment to extract electrolytes and prepare the byproducts for non-hazardous waste disposal.
- Non-recyclable waste is safely disposed of.
Limitations and Potential: Achieving High Battery Raw Material Recovery Rates
While it may not be possible to recover 100% of the battery raw material, Gazanfar highlights that recycling can achieve high recovery rates of up to 95%. Through the breakdown of batteries and the precipitation of salts, the impurities present in the materials, such as iron (Fe), copper (Cu), and magnesium (Mg), are also removed. These impurities can have a negative impact on the life and performance of batteries. However, utilizing multi-stage battery recycling methods allows for the extraction of high-purity materials, ensuring that the recycled materials are on par with newly mined metals.
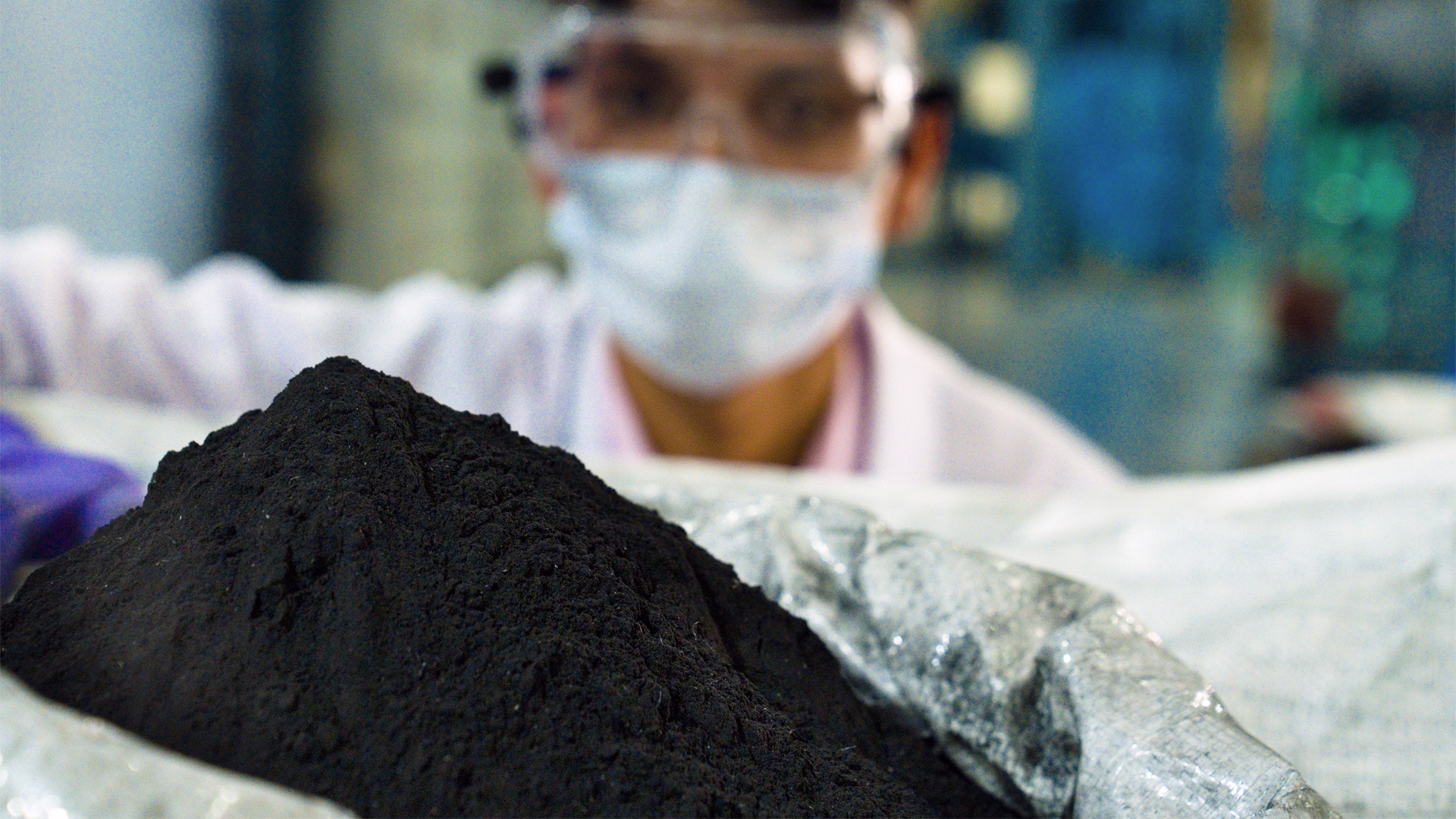
A study featured on McKinsey’s corroborates this with the projection that by 2040, 94% of all EV battery manufacturing feed-stock will primarily come from end of life batteries sent for recycling.
The Battery Raw Material Recycling Process & Technology Matter
One of the key challenges in recycling batteries raw material is the presence of impurities that affect the overall process. Gazanfar emphasizes that single-step recycling methods often lead to the precipitation of impurities, resulting in reduced battery life and performance. However, multi-stage battery recycling processes offer a solution to this problem. By employing advanced techniques, impurities can be effectively removed, enabling the production of high-quality recycled materials that can match the performance and longevity of mined metals.
Virtually Infinite Battery Recycling
The adoption of advanced battery raw material recycling techniques holds the promise of achieving a truly circular economy for battery materials. By recovering and refining materials from end-of-life batteries, the energy transition ecosystem can reduce its reliance on newly mined metals. These high-quality recycled materials can be used to create new batteries that are on par with those made from mined metals. This not only minimizes the environmental impact of mining but also ensures the longevity and sustainability of the energy storage industry.
Conclusion
The recyclability of lithium battery raw materials is a critical aspect of the sustainable energy transition. Through multi-stage battery recycling processes, such as those employed by LOHUM, it is possible to recover up to 95% of battery materials, including the conversion of extracted elements into salts and their subsequent recomposition into new batteries. By overcoming challenges and removing impurities through advanced battery recycling techniques, the potential of recycled materials that match the performance and lifespan of mined metals can be fully realized. Embracing multi-stage low-carbon battery recycling and investing in battery material recyclability R&D paves the way for a circular economy, where energy transition ecosystem assets can be recycled indefinitely, reducing the need for extensive mining activities, driving down the costs and CO2e of raw materials, and contributing to a greener future.
We hope that this in-depth exploration of battery raw material recyclability has brought to your awareness the immense potential and importance of battery recycling in achieving a sustainable energy transition. By understanding the processes and technologies that impact recyclability, the challenges involved, and the advancements in multi-stage recycling techniques, we can foster a #ClosedLoop economy of battery materials.
Keep up with LOHUM’s series on simplifying batteries and battery recycling, #BatteryDecoded, on our LinkedIn page for more insightful content on sustainability, battery energy, energy transition, circular economy, battery recycling, and battery repurposing.
Together, let’s drive the transformation towards a greener future, where resources are conserved, and the impact on the environment is minimized while maximizing value and utility. Browse LOHUM’s catalogue of recycled battery raw material here.
Related blogs
This entrepreneur wants India to make its own lithium-ion cells for electric vehicle batteries
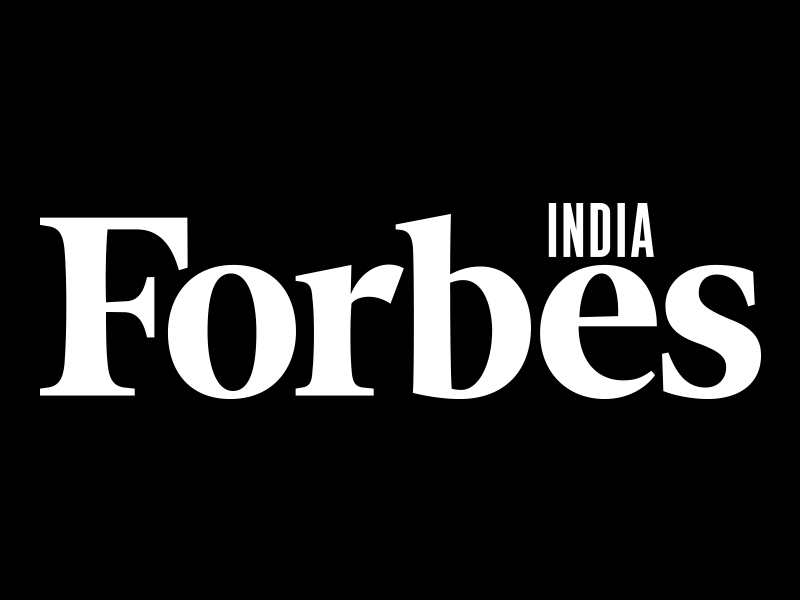
Forbes India
Rajat Verma already recovers raw materials from used cells at his venture, LOHUM Cleantech. He wants to close the loop by making cells in India as well.
India needs integrated recycling and repurposing battery business model: Rajat Verma of LOHUM Cleantech
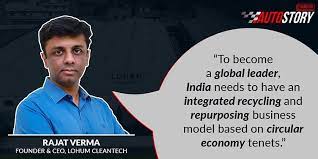
YOURSTORY
In an interaction with AutoStory, Rajat Verma, Founder and CEO of LOHUM Cleantech, speaks about building his company, and about battery manufacturing and repurposing as an industry.
Sourcing Raw Materials Is A Big Challenge In Li-ion Battery Space: Founder Lohum
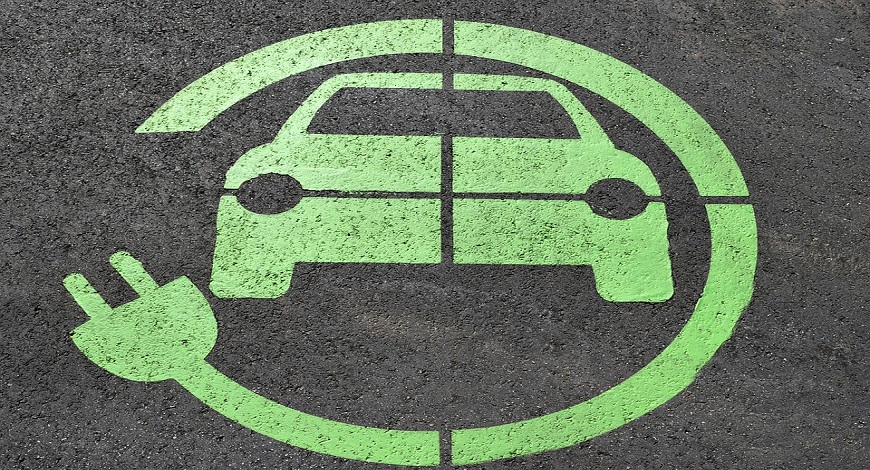
Business World Disrupt
Recognized as ‘The Most Innovative Company of the year 2022’ by The Confederation of Indian Industry (CII), LOHUM is a producer of sustainable Li-ion battery raw materials